The purpose of this independent tool is to calculate the homogenized macroscopic mechanical properties of a composite fold. From the mechanical properties of the fibers and the matrix, as well as the weaving pattern, the software calculates the mechanical properties of the fold, whether it is a 1D, 2D or 3D fabric.
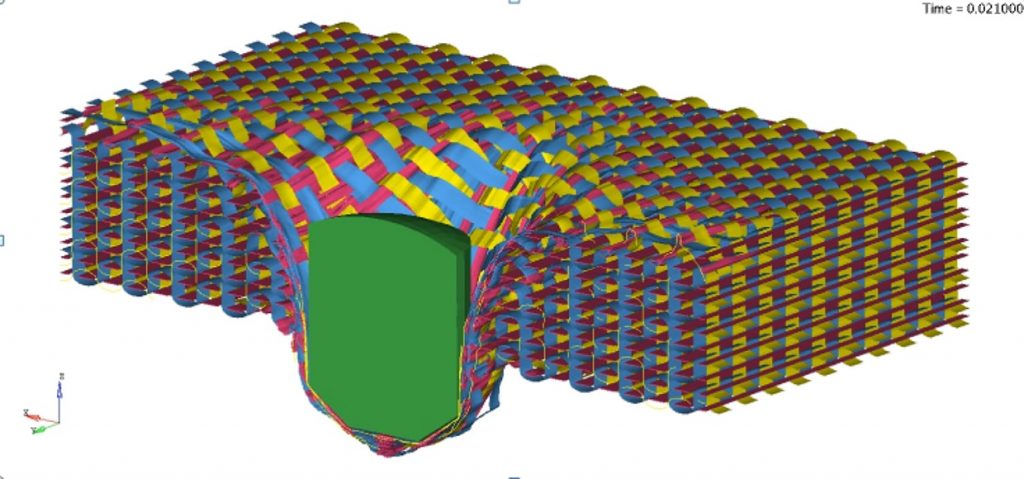